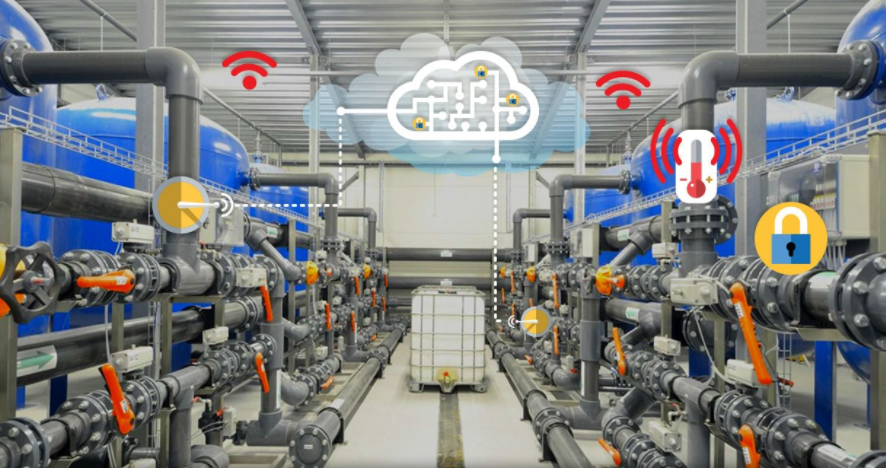
In sectors such as aerospace, automotive, logistics, transit management and process-driven manufacturing, the quest for efficiency and precision is unending. The integration of Bluetooth beacons into monitoring process control provides a significant leap in addressing these challenges. Traditionally, manual processes suffer from a range of issues. Bluetooth beacons offer a compelling solution to these age-old problems.
Firstly, there’s the matter of process visibility and optimisation. In complex environments like aerospace or automotive manufacturing, keeping track of components and processes is critical. Bluetooth beacons enable real-time tracking and provide data-driven insights, allowing for better decision-making and process optimisation. This technology ensures that every aspect of the manufacturing process is visible and under control, leading to enhanced efficiency and productivity.
A common issue in logistics and transit management is the misplacement of items; things can’t be located or are found in the wrong place. Bluetooth beacons counteract this by offering precise location tracking. This ensures that items are always where they need to be, thereby reducing the time and resources spent on locating misplaced items. In transit management, this translates to smoother operations and reduced delays.
Interaction, or the lack thereof, between components or processes, is another challenge that Bluetooth beacons can handle. In scenarios where two or more things are (or are not) interacting as they should, beacons provide real-time interaction data. This information is crucial in environments where the interplay between different components or processes is key to successful operations.
When it comes to counting, the issue often lies in having too many or too few items in a certain place. Bluetooth beacons facilitate accurate inventory management, ensuring that the right quantity of materials or products is always available where needed. This precision is particularly vital in just-in-time manufacturing processes, where inventory accuracy is paramount.
Time management is another critical factor in process control. A task taking too long or not long enough can significantly impact overall productivity. Beacons can track the time spent on specific tasks, providing insights into potential bottlenecks or inefficiencies. This data is invaluable for optimising workflow and ensuring that time is utilized effectively.
Lastly, sequence plays a pivotal role in manufacturing and logistics. When things happen in the wrong order, it can lead to a cascade of issues. Bluetooth beacons, with their ability to track and record sequences of events, ensure that processes follow the correct order, thereby avoiding costly mistakes and delays.