Our LocationEngine™ supports 2D as well as 3D locating. 2D is where only x and y are output and z, the height, remains constant. The advantage of 2D location is that it requires fewer locators (the hardware containing multiple antennas), only one per zone or room, rather than four or more. Also, the gateway and subsequent software receives correspondingly less data so, at the limit of throughput, many more assets can be supported.
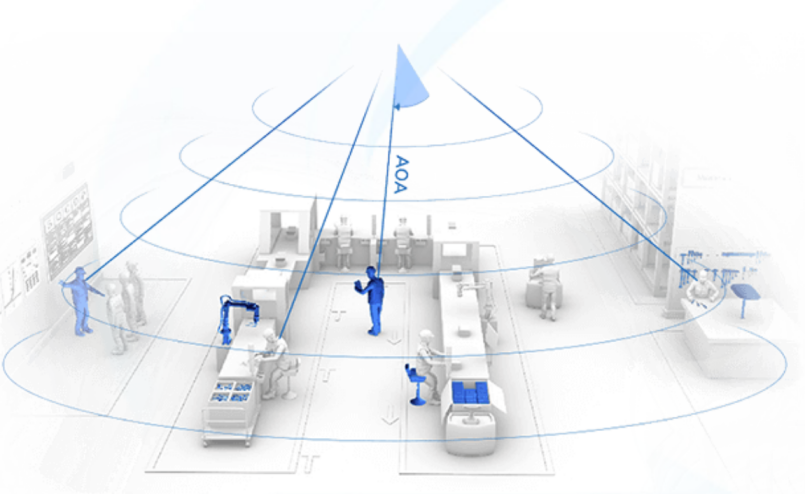
2D is only suitable if the z, the height, is known and doesn’t change much. For example, a beacon on a lanyard has restricted and fairly constant z. Conversely, a pallet in a tall warehouse might have a large variation in z and hence is not suitable for use with 2D locating.
As fewer locators are being used, the accuracy is poorer, of the order of a few metres rather than sub metre, than with 3D location. This kind of accuracy is sometimes an acceptable trade-off for less, lower-cost, hardware and a larger maximum number of assets.
In our LocationEngine™, the system is configured for 2D by setting a value in a configuration file and also supplying the typical z. This z is output in place of a calculated z. This value of z is actually used in calculations to provide x and y. This means if z does happen to change significantly from the value you have specified, the accuracy of x and y will be correspondingly poor.
Another aspect of 2D location is that it’s more sensitive to inaccurate initial measurement, usually performed using a laser measure, of location of the locators. When more than one locator is used in 3D locating, locator measurement error is less significant because the system calculation also depends on the location of other locators whose location measurement might be more accurate. With 2D location, the calculation is wholly reliant on the accurate measurement of one locator.
Read about PrecisionRTLS™